Home / All / Fine Chemicals / Continuous Flow Micro-Reaction Technology "HZSS Body" | Make Chemical Pharmaceuticals More Efficient And Safer
Continuous Flow Micro-Reaction Technology "HZSS Body" | Make Chemical Pharmaceuticals More Efficient And Safer

Continuous Flow Micro-Reaction Technology "HZSS Body" | Make Chemical Pharmaceuticals More Efficient And Safer
In the chemical pharmaceutical industry, the traditional kettle production method is still the main one, which has disadvantages such as long auxiliary operation time, high labor intensity for workers, difficulty in independent control, and slow mass and heat transfer.
Traditional batch production is prone to uneven temperature and concentration, resulting in low yield and poor product quality stability between batches. Especially when dealing with high temperature, high pressure, strong exothermic reactions and flammable, explosive, toxic, and harmful raw materials or intermediates, the traditional batch reaction process has problems such as difficulty in precise control and great safety hazards.
Continuous flow micro-reaction technology provides a new approach and method to solve the shortcomings and defects of traditional kettle synthesis. This technology can realize multi-step continuous flow automated synthesis and manufacturing from raw materials to API and even preparations through series or parallel reactors, without external intervention in the middle.
Compared with traditional kettle production, microchannel continuous flow skid-mounted equipment has the following advantages:
Higher production efficiency: The microchannel continuous flow skid-mounted equipment adopts a continuous production method. Compared with the intermittent production method of traditional kettle production, it has higher production efficiency and can greatly shorten the production cycle.
Lower energy consumption: The microchannel continuous flow skid-mounted equipment uses microchannel technology to achieve efficient heat and mass transfer, thereby reducing energy consumption and waste generation.
Higher product quality: Microchannel continuous flow skid-mounted equipment can achieve precise temperature and pressure control.
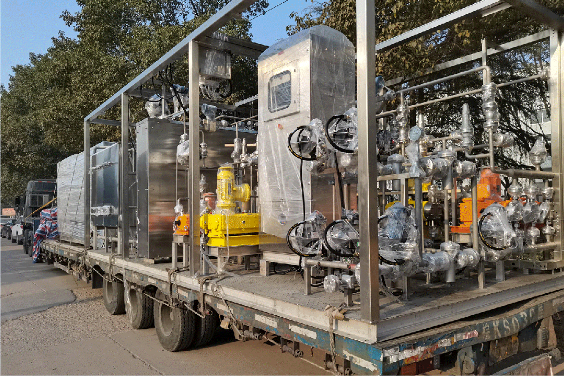
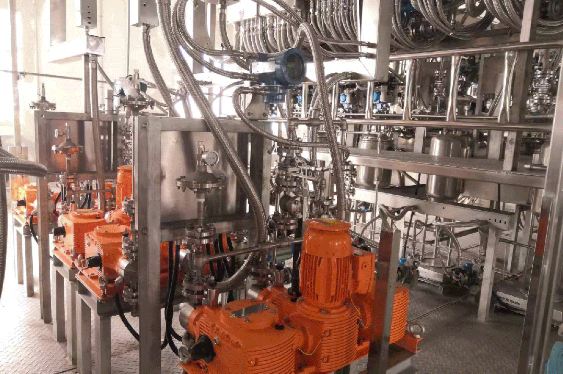


1. The delivery date is certain and short (3-4 months), saving a lot of time for customers' project construction;
2. Easy to move and install, and compatible with existing structures on the customer's site;
3. High integration, including automatic control system, SIS safety instrument system, automatic temperature control system and other facilities;
4. Off-site processing, short construction period, safer and more reliable quality.
Micro-Intelligence Project Case 1
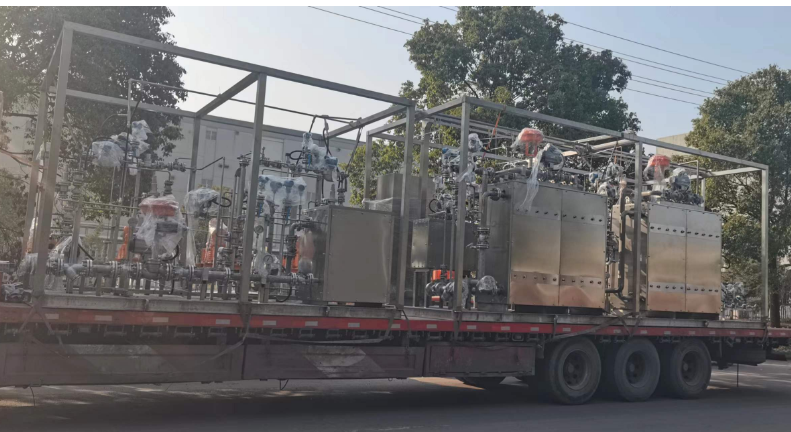
Micro-Intelligence Project Case 2
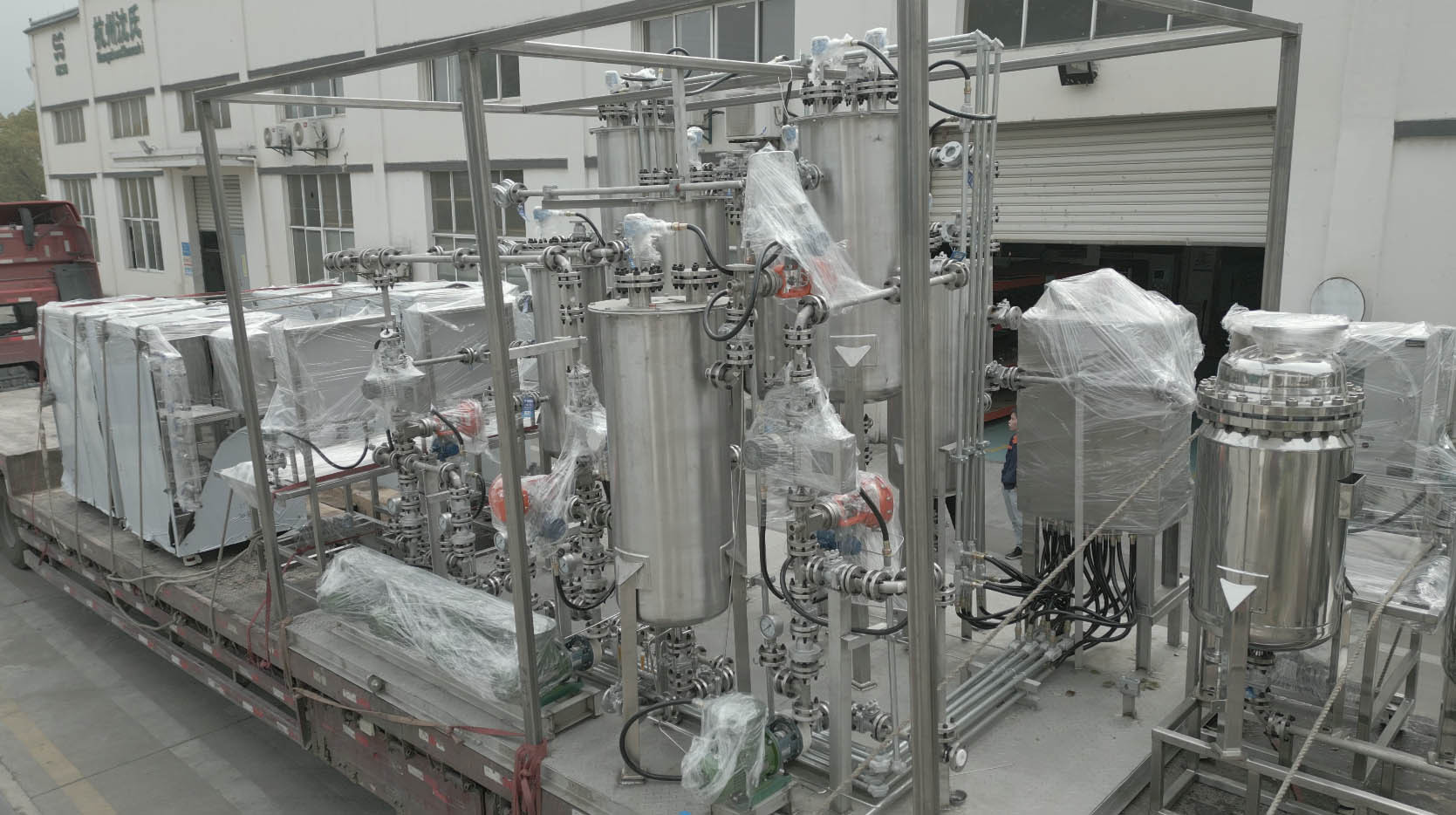
Flexible Experimental Platform
1. Process requirements for platform equipment: strong pressure bearing, strong heat exchange, strong corrosion resistance, continuous flow, multiple processes, multiple temperature zones, wide application range, mobility, system completeness, and aesthetics.
2. Device design
(1) Feeding skid: The device uses a diaphragm metering pump, a pressure transmitter and a flow meter made of HC276 or PVDF. Through PLC interlocking, it is combined into a skid to achieve quantitative, safe, stable and continuous feeding of materials within a predetermined flow and pressure range.
(2) Reaction skid: The device uses microchannel reaction plates in series, made of HC or SiC, and a dual-temperature zone independent branch oil circuit design to form a skid, which can meet the needs of a variety of materials, flow rates, and liquid holding capacity, dual-temperature zone independent heat exchange, and safe and efficient reactions under a wide range of flexibility.
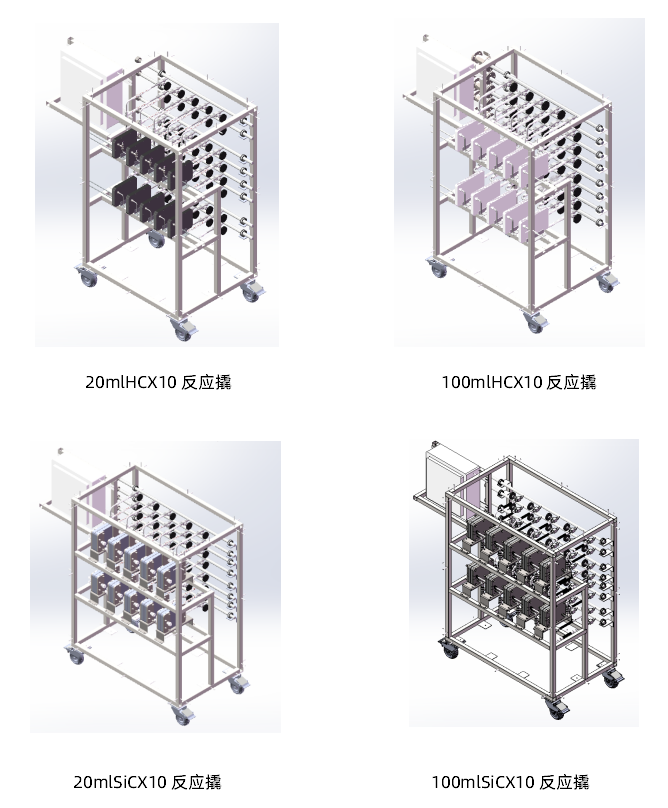
Continuous extraction
1. Equipment and process requirements: corrosion-resistant multi-stage continuous automatic extraction and separation at normal temperature and pressure.
2. Device design: The whole system adopts fluorine-lined storage tanks and pipeline accessories as well as PTFE pumps and other equipment resistant to dilute acid and chloride ions. U-shaped pipelines and storage tanks form an automatic stratification unit. Regulating valves, flow meters, and liquid level meters are equipped with PLC interlocking control to display relevant process parameters, so as to achieve the effect of multi-stage continuous extraction and separation.
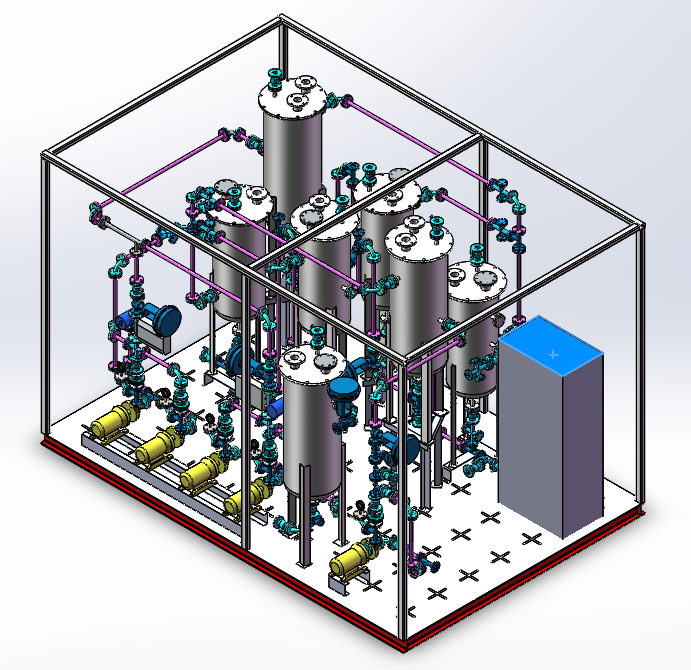
MAP01 Project
1. Equipment and process requirements: corrosion-resistant multi-stage continuous automatic extraction and separation at normal temperature and pressure.
2. Device design: The whole system adopts fluorine-lined storage tanks and pipeline accessories as well as PTFE pumps and other equipment resistant to dilute acid and chloride ions. U-shaped pipelines and storage tanks form an automatic stratification unit. Regulating valves, flow meters, and liquid level meters are equipped with PLC interlocking control to display relevant process parameters, so as to achieve the effect of multi-stage continuous extraction and separation.